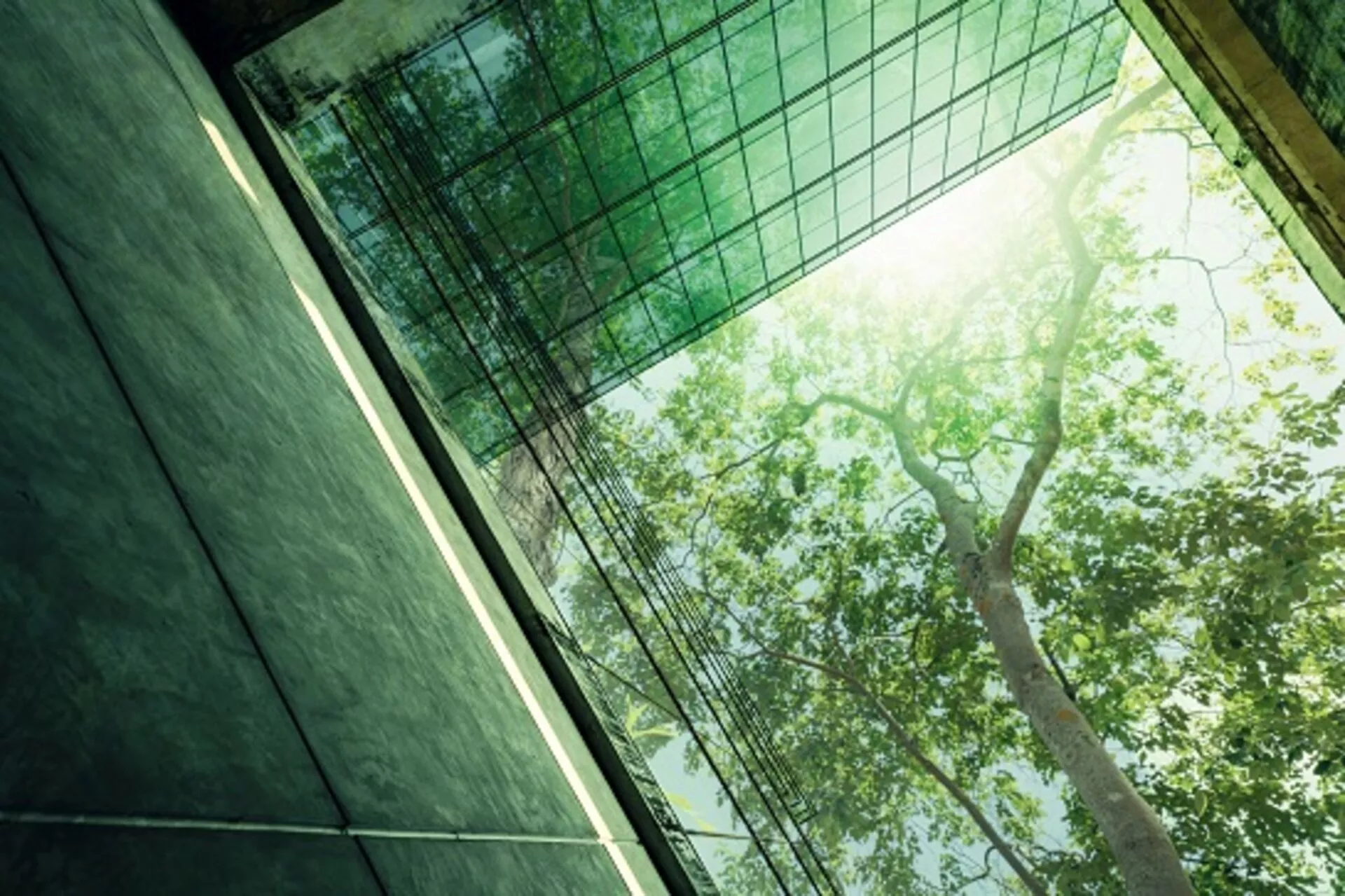
Stegra – Building a Decarbonised Steel Industry
Carbon dioxide emissions from steel are a major agenda point for both governments and environmentally conscious consumers who are committed to reducing their carbon footprints. How Stegra has financed the first steel plant that will remove almost all of these emissions from the steelmaking process?
By Christophe Hadjal, Managing Director and Regional Head for Europe, Batteries, Mining and Industries, Tim Hawk, Director, Batteries, Mining and Industries and Matthew Stewart, Director, Batteries, Mining and Industries, at Societe Generale.
Context and Transaction Rationale
Stegra was founded in the summer of 2020, a period during which global steel producers were suffering from low margins, encumbered balance sheets, and the effects of the global pandemic. In short, not the perfect conditions to build a new steel mill. But Stegra’s unique opportunity came out of a fourth, and ongoing challenge for the steel industry.
For European producers in particular, aligning an inherently carbon intensive process (between 7-9% of global anthropogenic emissions come from the production of steel) with the ambitions of the European Green Deal and the abatement commitments of their host nations and customers was becoming time critical.
Certain global producers had already taken the early steps in addressing this problem. The major advancement had been developing an alternative to the traditional blast furnace iron making route and its reliance on coal. Direct reduced iron (or DRI) is made by utilising reformed natural gas, instead of coal, whereby carbon monoxide and hydrogen react together with iron oxide in a reduction tower. The carbon intensity of the DRI process is approximately half that of the traditional blast furnace route.
DRI towers however require access to abundant, competitive natural gas, and would never solve the steel sector’s emissions problem alone, with material carbon dioxide emissions remaining. None had been built in Europe, where – as is the case globally – blast furnaces remain the dominant force in steel production. So, a further giant leap was needed.
To make that leap, Stegra’s founders asked why the carbon molecule could not be removed entirely from this reduction process to produce DRI. Hydrogen had already been proven to reduce iron ore at scale. So why hadn’t it replaced natural gas yet? The answer came down to three core challenges: pure hydrogen at scale was too expensive; customers were yet to acknowledge the required premium for green steel; and capital markets would not be ready to support development of a new integrated mill for a low-margin industry such as steel.
Stegra’s founders realised conditions were changing and all these challenges could be overcome. Fast forward three years, and they were proven spectacularly right with the signing of EUR 4.2 billion in green project financing facilities and the successful and record raising of EUR 2 billion in equity via private placement for their flagship green steel project in Boden, Northern Sweden. The project will produce 2.5 million tonnes of purely green steel each year, rising to 5 million tonnes after expansion, abating up to 95% of carbon emissions compared to the traditional blast furnace process.
How did they do this? In short, they constructed a valid business case that demanded financing, for both commercial and societal reasons.
Access the full article published in Project Finance International (PFI) - a subscription is required.